What Is Continuity In Business, And Why Is It Important?
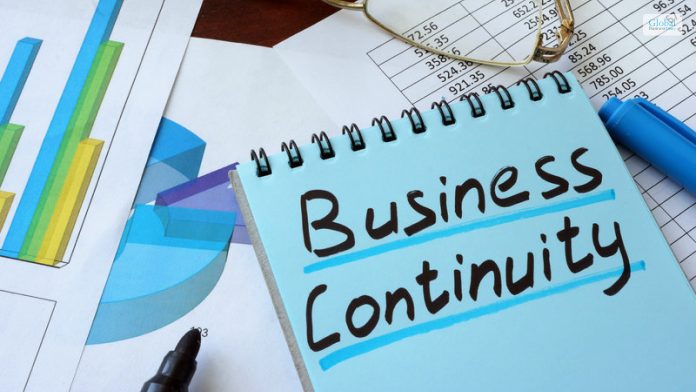
What is continuity? – In business, continuity means that the business is implementing procedures so that the organization can still operate near normal during a disaster or post-disaster. The disaster can range from natural disasters and man-made disasters to cyber-attacks and network errors. Hence, businesses create continuity plans where procedures of what to do is well-documented.
In this article, you will learn about what is business continuity and what are the major features of business continuity planning. Then, we will share with you the importance of business continuity planning and how your business can benefit from it. Then, you will also learn about the major constituents of continuity in business. Hence, to learn more about business continuity read on through to the end of the article.
What Is Continuity In Business?
According to Investopedia,
“A business continuity plan (BCP) is a system of prevention and recovery from potential threats to a company. The plan ensures that personnel and assets are protected and are able to function quickly in the event of a disaster.”
A business continuity plan is involved in creating a prevention and recovery system for the business so as to deal with the potential threats to the company. Apart from that, the continuity plan also helps to protect the assets and personnel of the organization and ensures that the organization functions appropriately.
A business continuity plan is also strongly tested so that there are no weaknesses in the system. This shall ensure that the organization can be able to take the right steps at the time of disaster. It is also important to define all the risks that can possibly affect the company at the time of disaster.
Importance Of Continuity In Business
Having a continuity plan is one of the most important steps that you can take for your business. The plan basically makes you look at the organization as well as yourself.
According to TechTarget.com,
“The plan should enable the organization to keep running at least at a minimal level during a crisis. Business continuity helps the organization maintain resiliency in responding quickly to an interruption. Strong business continuity saves money, time and company reputation. An extended outage risks financial, personal and reputational loss.”
The purpose of creating a continuity plan is to create and document procedures so that the company can respond to incidents. The plan is basically a guide that will give you instructions at the time of the disaster on how to operate. The guide is about how to manage and contain incidents and continue operations while there is a disruption of services.
For example, let’s assume a cyber attack disrupts the business network. You will then be forced to work offline. Here, a business continuity plan will help you to consider how you will continue operations and provide services to your customers or clients.
Creating a business continuity plan is also necessary to ensure legal compliance in many cases. Hence, you have to understand the regulations that can affect an organization’s processes.
What Are The Constituents Of Business Continuity?
According to LinkedIn.com,
“Business continuity planning involves conducting a complete analysis of your organization and all procedures, with clear guidelines on what to do during an incident. It also means implementing preventative measures to avoid incidents.”
The following are the major preventive measures you can take to avoid incidents:
1. Cloud Backup
You will need to back up all the essential data of your business to a cloud system. Hence, if your business system breaks down due to unavoidable circumstances, you can access your data from the cloud at times of need.
2. Analysis Of The Impact On Business
You will need to have an idea of the impact of the various disasters on your business work processes. You will need to consider who and what can be affected in the organization. Furthermore, you need to quantify the effects of them on your business.
3. Development Of The Business Continuity Plan
To do this step, you will need to have a full idea of all the processes in the organization. This way, you can develop a plan for your business and create procedures on how to respond to a disaster. Furthermore, you just need to create alternative arrangements for the continuation of the operations.
4. Implementation Of The Business Continuity Plan
The implementation of the business continuity plan consists of running drills in the business by creating a dummy situation of a disaster. In addition to this, you need to do incident response training in various other scenarios.
5. Training The Staff
To make your staff understand various threats that can arise at the time of disaster, you will need to provide training to your staff. This will give them a better understanding of when to do what and how to respond to the disaster situation in the organization.
Apart from the business continuity plan, you will also need to have a set plan, which you will need to review, test, and update on a regular basis. In addition to this, you will also need to communicate responsibilities to others, run practice drills, and evaluate procedures, as it is about how the personnel of the organization should act in times of crisis.
Hence, as you arrange for the management of the business continuity plan, you will need to review and update policies based on practice incidents for situations when threats really emerge. Hence, you will need to create steps as per your needs and demands.
Summing Up
What is continuity? – Hope you have found the answer to this question. You can see from this article that continuity is just a process in business. Here, the business creates continuity plans for the organization as a prevention and recovery system. This helps the business to deal with potential threats to the organization.
The business continuity plan provides a documented procedure and backup that helps the business to operate at the time of disasters or after them. Do you have any recommendations relating to the usage of a business continuity plan? Share your views and ideas with us in the comments section below
Read More: