Trends In The Aluminum Extrusion Markets And Its Role In Modern Manufacturing
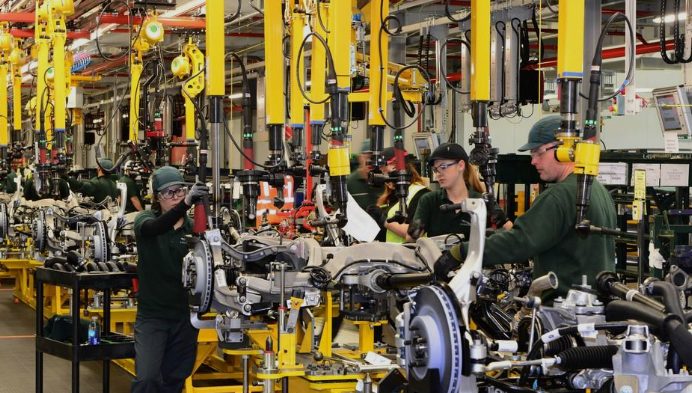
As modern manufacturing looks back on its history, one metal, in particular, stands out as one that made a tremendous impact on the world we live in today. That metal is Aluminum.
Perhaps second only to steel, aluminum, of all other metals, has been a versatile metal that impacts many aspects of the manufacturing process. Factories of all sizes and types employ aluminum in building products that are essential to everyday life. Whether it is a car, an airplane or a spaceship, aluminum is sure to be found as one of the essential building elements of all of these modern-day marvels that make our life easier and allow us to be transported from one place on the planet to another in mere hours rather than weeks. One of the companies leading the charge towards this is http://signaturealum.com which is leading the way towards more sustainable and technological trends in the industry. So, what are some of the trends and recent technological advances that have made this metal even more versatile and an essential element in the modern manufacturing process?
What Is The Extrusion Process?
Aluminum extrusion is a manufacturing technique that has revolutionized modern manufacturing. It involves pushing aluminum alloy through a designed tool to create specific profiles with precise dimensions. The process starts by heating the aluminum billet to a temperature that makes it easily moldable. The temperature that is required for this is very high, then the heated billet is loaded into the extrusion press where it is forced through the tool to give it the desired shape. This method allows for the production of profiles with a wide variety of shapes and sizes, such as rods and tubes. It is also possible to produce complex and customized designs. Achieving precision involves controlling factors like temperature, pressure, and speed during extrusion. Once extruded, the profiles are allowed to cool down first, and then they are cut into desired lengths and often undergo heat treatment for improved properties. The end result is an extruded aluminum profile that offers strength, lightweight characteristics, and excellent resistance against corrosion.
Trends In The Industry
The aluminum manufacturing and extrusion industry has seen recent growth and changes in times influenced by several key trends shaping the modern manufacturing landscape. Industries around the globe are increasingly adopting sustainability and efficiency making the aluminum market a key area for increased demand and for advancements. What are some of the key elements that are driving this increased demand?
Increased Demand For Lightweight And Sustainable Materials
One of the factors driving the expansion of this versatile industry is the increased need for materials that are both lightweight and environmentally friendly. Industries such as automotive, aerospace, construction, and electronics are actively seeking ways to reduce weight and enhance fuel efficiency. Aluminum has become a leading choice for many of these applications due to its strength-to-weight ratio, making it an ideal candidate for the most sophisticated applications that require strong metals. It should be no surprise that there is a shift towards using materials like aluminum to address concerns about sustainability in manufacturing processes.
Advancements In Technology
Technology plays a role in fostering innovation across industries including the key industry of manufacturing aluminum alloys. With advancements in computer-aided design (CAD) software and simulation tools, manufacturers can now design shapes with precision. They can also optimize their production processes for improved efficiency and adherence to customer requirements. Specifications that would have been impossible to manufacture in the past are now easily possible due to this explosion of technological advances in the manufacturing process. Additionally, digitalization has enabled real-time monitoring of production lines, resulting in quality control measures that further increase efficiency and reduce waste.
Sustainability At The Forefront
Sustainability has become a focus of many governments in the past decade, and this also holds true in the aluminum extrusion industry with businesses that have been paying attention to ecofriendly practices. Aluminum is known for its recyclability, which is great for the environment and improves energy efficiency. As environmental concerns continue to rise companies are embracing approaches making aluminum extrusions an option for consumers who care about the environment.
Expanding Global Market
The market for aluminum extrusion is witnessing growth in regions in emerging markets and across the world. Developing countries are investing in infrastructure and industrial development leading to an increased demand for aluminum extruded products across sectors like construction and transportation. This expansion presents opportunities for both established and emerging players in the market.
As the realm of the aluminum industry expands into new markets, it involves reaching out to customers and industries in various locations around the world. This trend reflects the growing demand for aluminum extruded products on a level that is driven by factors like infrastructure development, industrialization, and a stronger focus on materials. As the aluminum extrusion industry expands worldwide, manufacturers and suppliers are exploring emerging markets, forming partnerships, and adjusting their strategies to meet the requirements and regulations of regions. This expansion brings in additional sources of revenue, and it also encourages collaboration and the exchange of technologies, ultimately contributing to the industry’s overall growth and competitiveness on a global scale.
Enhance Customer Capabilities
In today’s market, customers have higher expectations when it comes to customizing products. This holds true for industries that rely on aluminum profiles since they seek tailored solutions that not just meet their specific requirements but also improve efficiency and remain cost-effective. The emergence of techniques like port die technology has played a significant role in facilitating this customization process.
The aluminum market is constantly expanding and improving, which creates new possibilities for products and materials that would have been undreamt of in the past. The industry is trending to continue upward, and these trends suggest a dynamic future. With a focus on sustainability and advancements in technology the industry is adjusting to meet the needs of sectors. Whether it’s in automotive, aerospace, construction, or other industries, aluminum extrusions are becoming a part of manufacturing. This aligns directly with many businesses and government incentives on sustainability, technological advances, and improvements.
Read Also:
- Boxed Packaged Goods: The Right Guide To Uplift Your Business
- How To Ensure Your Warehouse Is Safe To Work In
- How To Boost Warehouse Productivity